The turret is one of the most essential components of tablet compression machines, responsible for rotating and synchronizing punches and dies for tablet formation. The turret’s design and functionality are closely linked to other key components of the machine, including the feeder, cam tracks, punches, and dies. Proper integration of the turret with these components ensures smooth operation, higher productivity, and consistent tablet quality. This article explores the importance of turret integration, its role in synchronizing various parts of the machine, and the benefits of seamless operation.
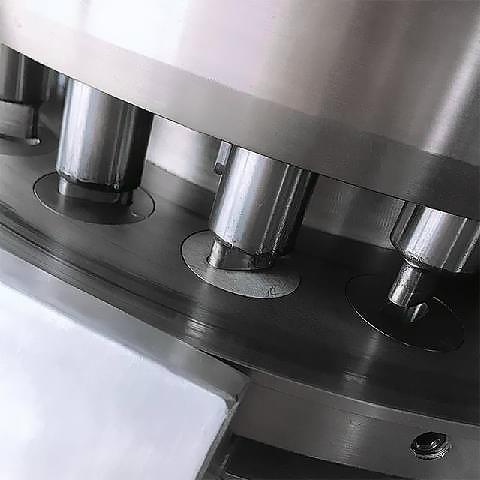
Turret and Feeder Interaction
One of the primary functions of the turret in a tablet compression machine is to work in tandem with the feeder to ensure a continuous flow of material into the die. The feeder supplies powder or granules to the dies through a carefully controlled process, and the turret ensures the even distribution of the material for consistent tablet formation.
1. Material Consistency: The turret helps synchronize the movement of the feeder with the punches, ensuring that each die is filled evenly and consistently. A well-integrated turret ensures that the material flow remains constant, reducing the likelihood of under-filled or overfilled tablets.
2. Feeder Control: The turret’s rotation speed and timing are coordinated with the feeder's operation. This coordination is critical in maintaining the optimal fill level and ensuring no material waste.
3. Precise Material Placement: A well-functioning turret can ensure that the material is accurately placed into the dies, which is crucial for tablet uniformity, especially when dealing with small quantities of high-potency drugs or delicate formulations.
Coordination with Punches and Dies
The turret plays a vital role in coordinating the punches and dies, ensuring that the tablet is formed consistently and precisely with every cycle. Turrets rotate at specific speeds and intervals to align the punches and dies in the proper configuration for compression.
1. Synchronization for Tablet Formation: The turret ensures that the punches move up and down at the right moments to compress the material into tablets. The timing and coordination between the turret and the punches are crucial to achieve a uniform tablet size, weight, and shape.
2. Efficient Compression: The turret's rotation must be perfectly aligned with the punches' motion to apply the right amount of compression force at the right time. If the synchronization is off, it can lead to defects in the tablets, such as inconsistent compression or improper tablet hardness.
3. Preventing Jams: Proper turret integration ensures smooth movement of the punches and dies. Misalignment between the turret and other components can result in jamming, causing delays in production and potential damage to the machine.
Role of Cam Tracks in Turret Operation
Cam tracks are integral to the operation of the turret, guiding the movement of the punches during tablet formation. These precision-engineered tracks direct the punches through various stages of the compression cycle, ensuring the correct sequence of actions.
1. Guiding Punch Movement: Cam tracks control the height at which punches engage the dies and the force with which they compress the material. The turret follows the path set by the cam tracks, ensuring accurate and reliable punch movement throughout the cycle.
2. Cam Track Precision: The precision of the cam tracks directly impacts the efficiency of tablet formation. Accurate cam tracks ensure that the punches perform consistently, leading to high-quality tablets with uniform size and shape.
3. Reducing Friction and Wear: Proper integration of the cam tracks with the turret helps reduce the wear and tear on both the turret and the punches. This integration minimizes friction, extends the life of the components, and ensures smoother operations.
Turret Speed and Compression Pressure
The speed at which the turret rotates is closely linked to the compression pressure applied to the tablet. This synchronization is critical for producing tablets with the correct density and hardness, ensuring that the product meets the required standards.
1. Optimal Speed for Compression: The turret’s rotation speed must match the required compression force to achieve consistent tablet formation. A slower speed may result in insufficient compression, while a faster speed may lead to over-compression or defects in tablet consistency.
2. Compression Adjustment: Adjusting the turret speed in relation to compression force helps ensure that each tablet undergoes the correct amount of pressure during compression. This is particularly important for producing tablets with a precise weight, hardness, and dissolution profile.
3. Preventing Tablet Defects: Proper synchronization between turret speed and compression pressure helps prevent tablet defects such as cracks, chips, or inconsistent weight, ensuring that every tablet meets the required quality standards.
Ensuring Smooth Operation for Seamless Production
One of the primary benefits of turret integration is the ability to ensure smooth operation throughout the tablet manufacturing process. Proper turret integration with other components prevents delays, minimizes the chances of machine downtime, and ensures consistent output.
1. Minimizing Downtime: When the turret is well-integrated with the feeder, punches, dies, and cam tracks, the entire compression process runs smoothly. This minimizes machine downtime, which can significantly increase productivity.
2. Consistency and Quality Control: Proper turret integration guarantees that tablets are formed consistently throughout the production run. With fewer production interruptions and defects, manufacturers can achieve higher output and meet strict quality control standards.
3. Troubleshooting and Adjustments: Seamless integration allows for easier troubleshooting and adjustments. If an issue arises, it is easier to identify and correct the problem when the turret is correctly synchronized with the rest of the components.
Conclusion
Turret integration is a critical aspect of tablet compression machine performance. The interaction between the turret, feeder, punches, dies, and cam tracks ensures smooth, efficient tablet formation and high-quality output. Proper synchronization of the turret’s rotation speed, compression pressure, and material flow is essential for optimal production. By focusing on seamless integration, manufacturers can improve efficiency, minimize downtime, and maintain the consistent quality of their tablets.
Related Questions
1. What is the role of the turret in tablet compression machines?
The turret coordinates the movement of punches and dies, ensuring that the tablet is formed consistently and efficiently.
2. How does the turret synchronize with the feeder?
The turret works in tandem with the feeder to ensure a consistent and precise flow of material into the dies for tablet formation.
3. What is the importance of cam tracks in turret operation?
Cam tracks guide the punches through various stages of compression, ensuring the correct application of pressure and movement for accurate tablet formation.
4. How does turret speed affect tablet quality?
The turret speed must be synchronized with the compression force to ensure that the tablets are compressed to the correct density, hardness, and size.
5. What are the benefits of proper turret integration?
Proper turret integration ensures smooth operation, higher productivity, fewer defects, and consistent tablet quality.
If you need more information on optimizing turret integration for your tablet compression machine or require assistance with your production line setup, don’t hesitate to reach out to us. We're happy to help you improve efficiency and ensure consistent tablet quality!