In pharmaceutical manufacturing, tablet quality is non-negotiable. Defects like capping, chipping, sticking, and mottling are common. These issues affect the tablet’s effectiveness and safety.
Tablet defects occur for several reasons: poor formulation, faulty equipment, and process errors. Knowing the defects, their causes, and remedies is key to maintaining high-quality tablets. Here are the 15 most common defects and how to tackle them.
Tablet Defects
1. Capping
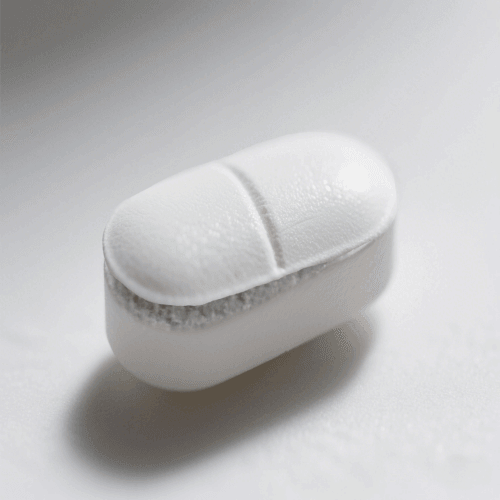
Definition: Capping is when the tablet’s top layer separates from the body, leaving a concave space.
Cause: Air trapped during compression, weak binding, or over-dried granules.
Remedy:
- Granulation: Increase binder concentration to improve cohesion.
- Compression: Adjust pre-compression force to expel trapped air.
- Equipment: Maintain punches and dies to prevent malfunctions.
2. Lamination
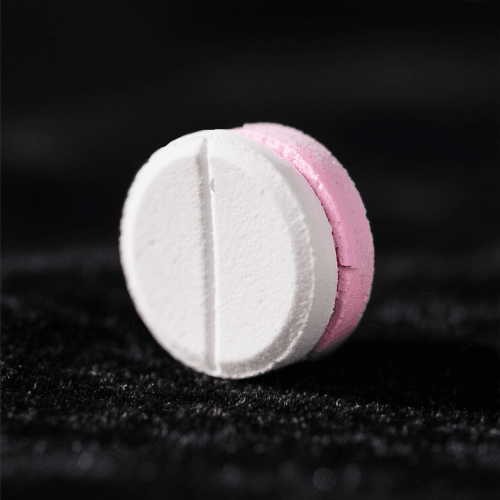
Definition: Lamination occurs when a tablet forms layers, with weak bonding between them.
Cause: Rapid decompression or weak layer bonding.
Remedy:
- Compression: Slow down the compression speed to allow uniform bonding.
- Granulation: Ensure uniform particle sizes for better bonding.
3. Chipping
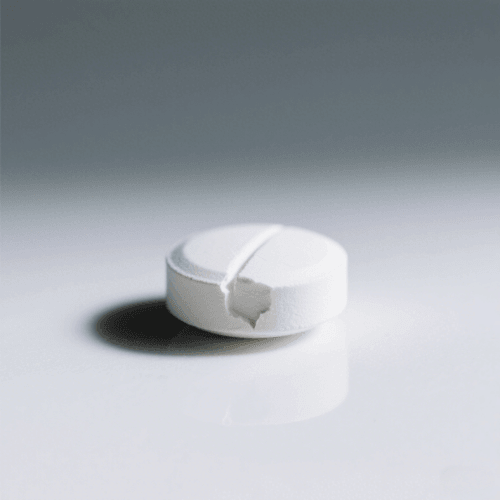
Definition: Chipping is the breaking of tablet edges or corners.
Cause: Low moisture, excessive friability, or worn tooling.
Remedy:
- Granulation: Adjust moisture levels.
- Equipment: Replace worn punches and dies.
4. Sticking
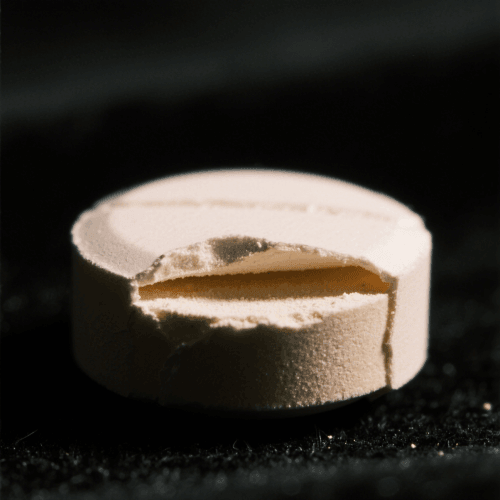
Definition: Sticking happens when tablets adhere to punches or dies.
Cause: Excessive moisture or poor lubrication.
Remedy:
- Granulation: Control moisture levels.
- Compression: Use suitable lubricants to reduce adhesion.
5. Mottling
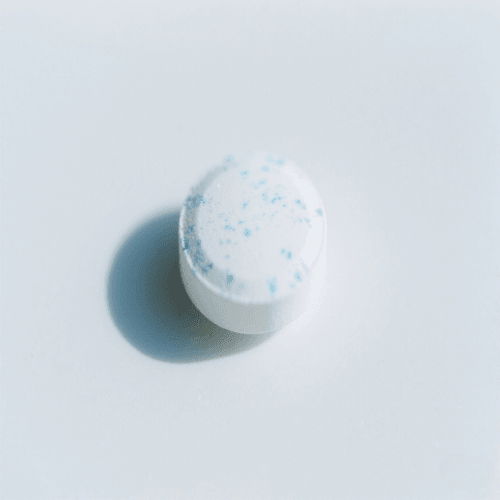
Definition: Mottling refers to uneven coloring, leaving blotchy or streaky marks.
Cause: Uneven distribution of colorants or dye migration.
Remedy:
- Blending: Mix colorants thoroughly.
- Drying: Control drying temperature to prevent dye migration.
6. Double Impression
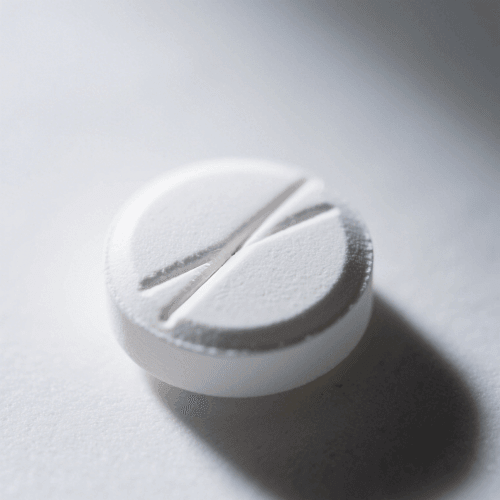
Definition: Double impression occurs when two overlapping imprints appear on a tablet.
Cause: Misaligned punches during compression.
Remedy:
- Equipment: Use keyed punches to prevent rotation.
- Maintenance: Inspect punch alignment regularly.
7. Cracking
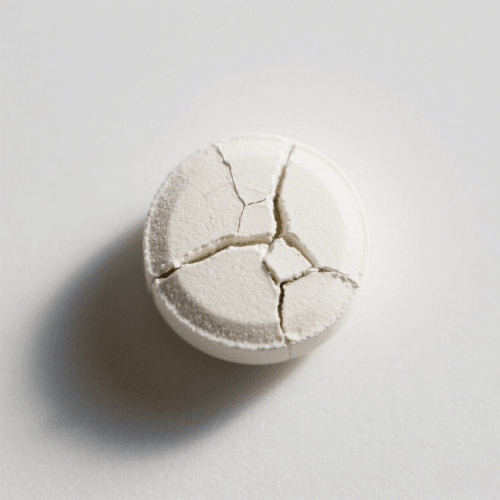
Definition: Cracking occurs when a tablet splits or fractures after compression.
Cause: Rapid expansion post-compression or during coating.
Remedy:
- Compression: Adjust compression force to optimal levels.
- Coating: Control drying rates to avoid rapid tablet expansion.
8. Binding
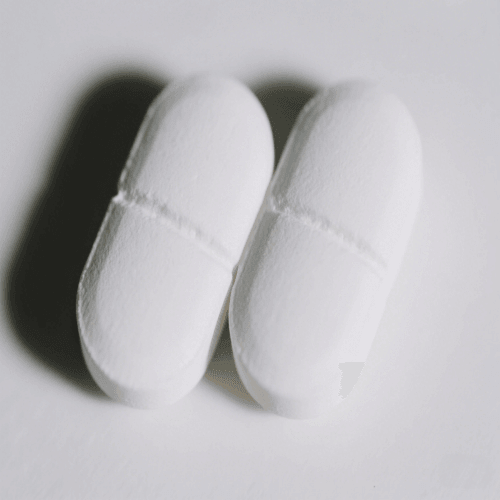
Definition: Binding defects occur when tablets experience excessive friction against the die walls.
Cause: Poor lubrication or die imperfections.
Remedy:
- Compression: Use suitable lubricants.
- Equipment: Maintain smooth, defect-free dies.
9. Blistering
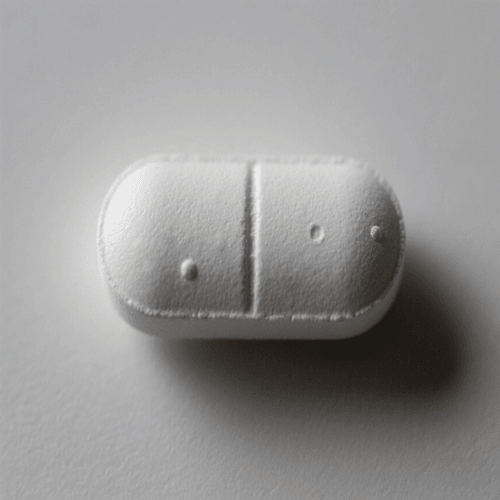
Definition: Blistering occurs when trapped gases form bubbles under the tablet’s coating.
Cause: Entrapped gases during coating.
Remedy:
- Coating: Optimize drying temperature and airflow to release gases.
10. Flaking
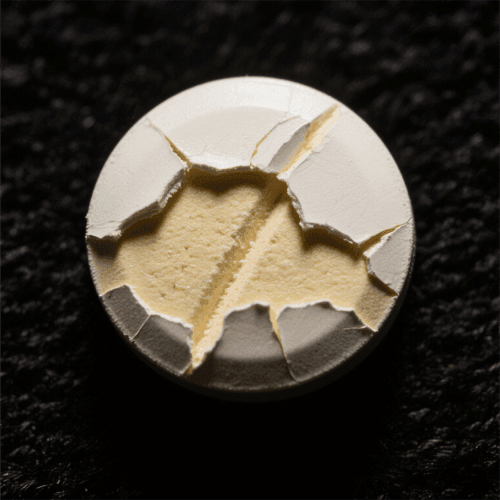
Definition: Flaking happens when the coating of a tablet begins to peel off.
Cause: Weak coating adhesion.
Remedy:
- Coating: Adjust the formulation to improve adhesion strength.
11. Hardness Variation
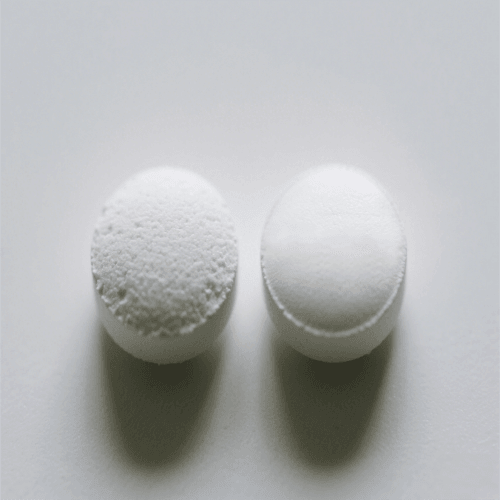
Definition: Hardness variation refers to differences in tablet hardness within the same batch.
Cause: Inconsistent compression force or particle size.
Remedy:
- Compression: Calibrate compression force regularly.
- Granulation: Ensure uniform granule sizes.
12. Weight Variation
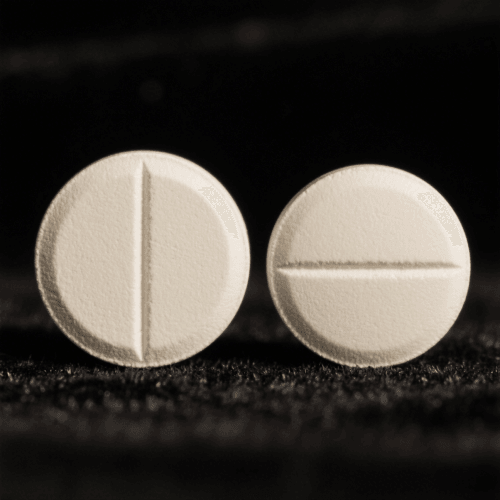
Definition: Weight variation refers to inconsistency in the weight of tablets within a batch.
Cause: Poor granule flow or inconsistent die fill.
Remedy:
- Granulation: Optimize granule flow.
- Equipment: Use force feeders for consistent die filling.
Tablet manufacturing is a complex process. A slight deviation can lead to defects, risking product quality and patient safety. While common issues like capping, sticking, and weight variation are well-known, a deeper understanding of how equipment, quality standards, and detection systems interplay is essential.
This article builds upon the basics of tablet defects. It explores the relationships between machine types and defect types, risk classification from a QA viewpoint, the evolution of monitoring systems, and compliance guidance based on global GMP standards.
Equipment-Type Defect Correlation
Single Punch vs. Rotary Tablet Press
Single-punch presses, while simple and economical, are more prone to weight variation and lamination due to inconsistent feed and slower compression cycles. Rotary presses, especially with multi-tip tooling, can produce tablets rapidly but may introduce problems like double impressions or tooling wear.
Single Punch Machines:
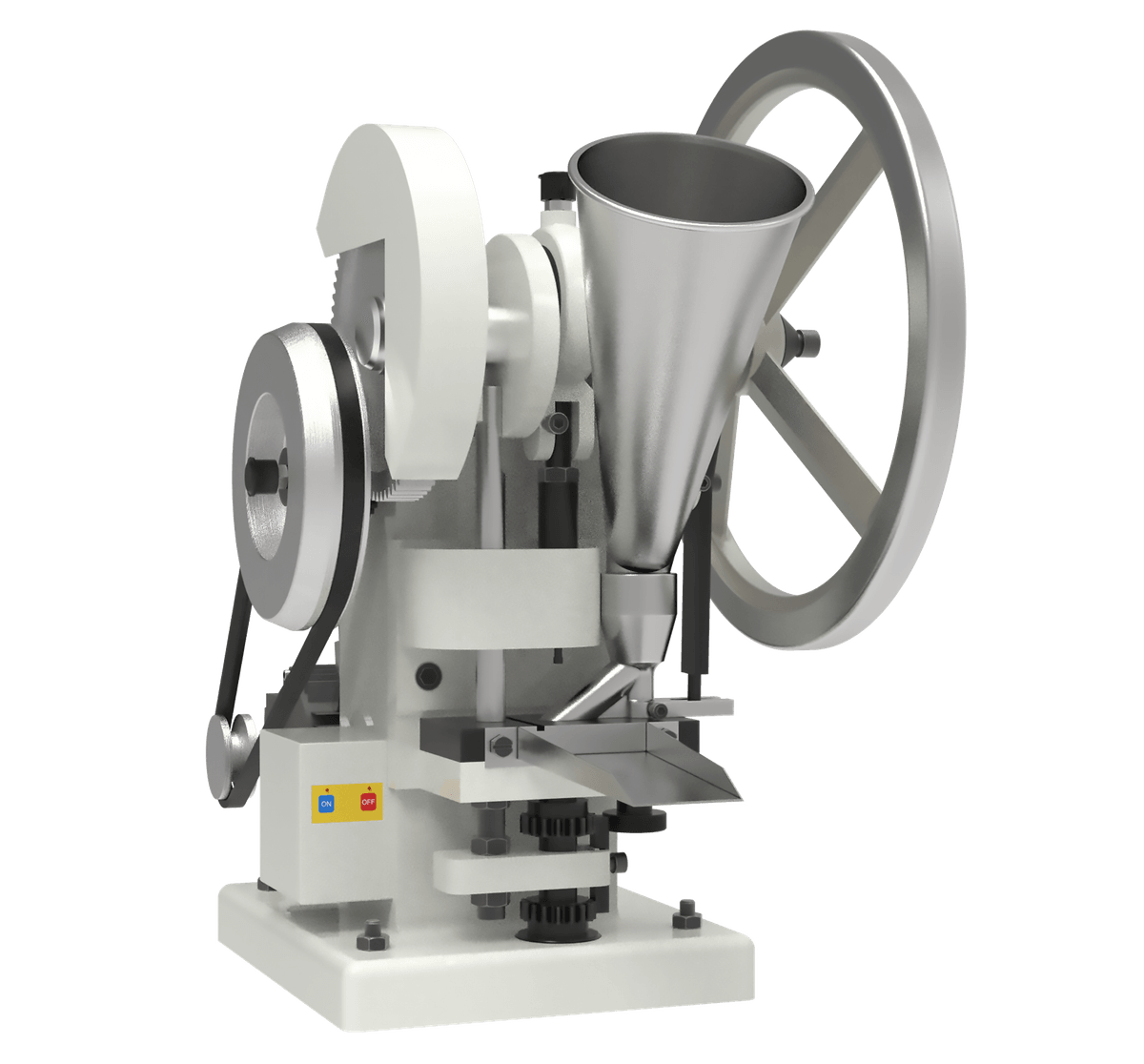
- More likely to cause lamination, capping.
- Less suitable for high-speed production.
Rotary Presses:
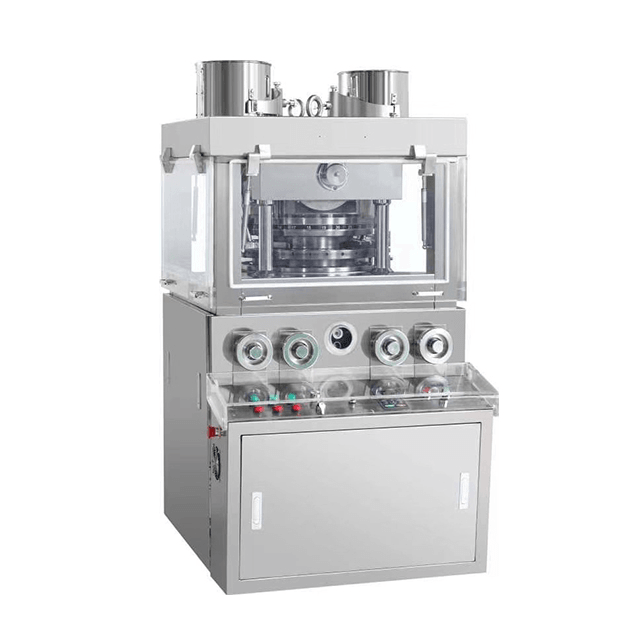
- Require strict maintenance to prevent double impression.
- Better suited for automation and integration with feeders.
Forced Feeder Systems
A forced feeder ensures consistent material flow into dies, reducing weight variation. In poorly flowing powders, gravity feeders lead to under-filling, especially in high-speed rotary presses. Forced feeding reduces the risk of rejected batches due to tablet weight failure.
Tooling and Surface Treatment
The design and surface finish of punches and dies greatly impact chipping and sticking.
- Polished surfaces reduce friction and prevent powder from adhering.
- Coated tooling (e.g., TiN or DLC) resists picking and extends punch life.
- Embossed punches need more attention, as they often attract sticking.
QA-Based Risk Classification of Defects
Appearance vs. Functional Defects
Defects differ not just in appearance but in impact:
- Appearance-only: Mottling, slight chipping, surface scratches.
- Functional impact: Capping, erosion, delayed disintegration.
Acceptable vs. Rejectable
- Cosmetic-only defects may be accepted under deviation with justification.
- Defects impacting dose uniformity, stability, or release profile must result in rejection or rework.
GMP-Based Defect Classification System
- Establish a visual defect catalog (with images, samples).
- Define severity grades: Critical, Major, Minor.
- Link each to disposition rules: Rework, Reject, or Pass with justification.
- Document decisions within the QMS and deviation records.
Detection and Monitoring Systems
Lab-Based Testing
- Weight Variation (10-tablet average and RSD tracking)
- Hardness Testing (Mechanical testers with digital log)
- Disintegration & Dissolution Tests (linked to batch release)
Automated Visual Inspection
Modern systems use high-speed cameras and image processing to identify:
- Cracks, foreign particles, engraving defects
- Color inconsistency (mottling, specks)
In-Line Weight & Compression Force Monitoring
- Load cells under punches track compression force in real-time.
- Statistical feedback loops allow auto-adjustment to feeders.
- Weight reject systems eliminate off-spec tablets instantly.
GMP-Compliant Defect Control (US & EU Focus)
21 CFR Part 210/211 Guidance
- Process Validation: Equipment qualification and process mapping.
- In-Process Controls (IPC): Real-time checks of weight, appearance, hardness.
- Documentation: Batch records, deviation reports, OOS handling.
EMA/FDA Audit Concerns
- Recurrent sticking without corrective action.
- Poorly maintained tooling.
- Incomplete root cause analysis of defects.
Recommendations
- Create defect trend charts.
- Implement preventive maintenance schedules.
- Integrate automated systems for real-time rejection.
- Include defect rates in APR/PQR reviews.
Addressing these defects starts with understanding the underlying causes. Optimizing granulation, ensuring regular equipment maintenance, and calibrating compression forces are just a few ways to reduce defects. By diving deeper into specific stages of production, manufacturers can fine-tune processes for optimal tablet quality.
Related Topics and Answers
1. How does granule moisture content affect tablet quality?
Moisture content impacts compressibility. Too much moisture leads to sticking, while too little can cause capping and chipping.
2. What role does punch and die maintenance play in preventing defects?
Maintaining punches and dies ensures smooth surfaces and proper alignment, reducing defects like sticking, picking, and double impressions.
3. How can formulation adjustments mitigate tablet defects?
Tweaking excipient ratios, binder types, and lubricants can improve tablet quality and minimize defects.
4. Why is compression force calibration important?
Proper calibration ensures uniform tablet hardness and weight, reducing defects like capping, lamination, and weight variation.
5. What are the benefits of using advanced coating technologies?
Advanced coatings protect active ingredients and improve tablet appearance, while reducing defects such as blistering and flaking.
Tablet defects are a challenge in pharmaceutical manufacturing. But by understanding their causes and applying the right remedies at each stage of production, you can improve tablet quality. Formulation, process control, and equipment maintenance are all key to achieving the desired results.
For pharmaceutical manufacturers looking to enhance tablet quality, explore advanced tablet press technology and formulation development. Contact us today for customized solutions tailored to your production needs.